Most organizations see only a tiny amount of the potential benefits of a value stream improvement effort built around a mapping exercise. Such an exercise can be a powerful organizational development tool as well as one for improving value-stream performance on quality, efficiency, and safety. However, before you embark on such an endeavor, here are 10 key things to keep in mind:
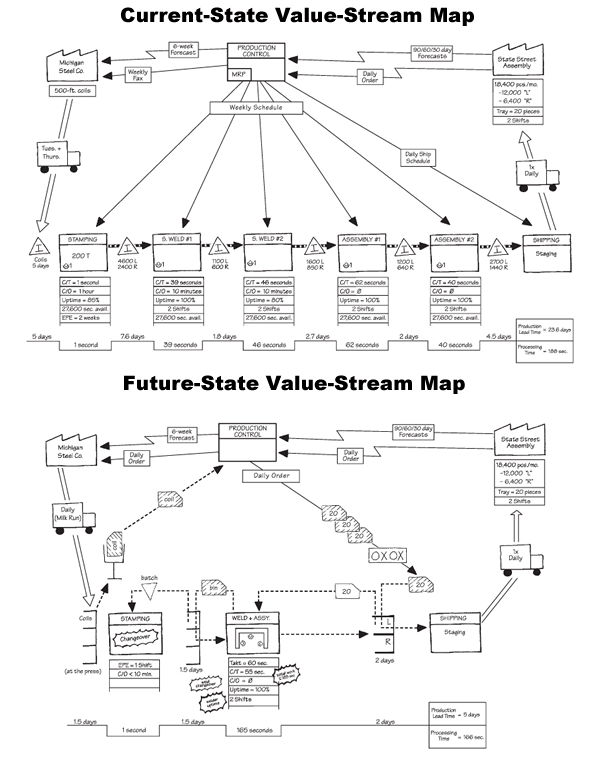
1. Pick Processes (Value Streams) That Matter
In other words, select value streams (or value-stream segments) that link to your strategic plan, annual goals, balanced scorecard performance, etc. Doing this means you must be clear about your customers, what they require from these value streams (not programs) by which you deliver value to them, and how well those streams are currently performing. Publicly funded companies may also have other stakeholders to consider as well. Picking value streams that impact organizational performance will help justify the time and effort required to map well and improve the work.
2. Start With a Win — For the People Doing the Work
Lean management is full of paradoxes, and here is one. Sometimes you may need to select a value stream for improvement based on the potential impact on your employees. Choosing to map and improve a value stream to benefit employees is especially important when people are just learning the lean improvement methodology. For example, it’s not by accident that CEO Paul O’Neill started his turnaround at Alcoa with a focus on employee safety. Once he demonstrated that commitment, he got full cooperation for other improvement efforts from the union and workers on the front lines. Likewise, starting with a value stream to reduce high employee dissatisfaction or undesired turnover builds support for future improvement efforts.
3. Be Clear About Scope — And Don’t Creep!
We all want to end world hunger and achieve world peace — but without focus, we won’t achieve anything. Most high-level value streams are really more like value rivers. Sorting out the major contributing streams and identifying those that need to be improved to impact organizational performance increases the value of your mapping and improvement efforts. And determining up front where the value stream starts and stops and what is in and out of scope for people doing improvement work prevents a lot of wandering in the wilderness. Address these and other issues before you start a mapping exercise in the form of a Value Proposition or Team Charter.
4. Get the Right People on the Bus
Involve the value-creators — the people closest to the work process you’d like to improve (at whatever level that work is performed) and in all the critical processes involved in developing the map(s), defining problems, and crafting solutions. See together, learn together, act together, and improve together. And, wherever possible, ensure to include suppliers and customers, not just doers. If you have to map with a small group, make sure you socialize their draft products with the value creators for the value stream. Keep a regular communication link to all levels of the organization.
5. GO AND SEE how it’s really done!
Supplement spreadsheet data with direct observation and interviews at the gemba. You’ll be amazed at the things you learn that never appear on spreadsheets.
6. Eat the Elephant One Bite at a Time — but Plan to Eat It All — or at Least As Much as You Need
As you begin your improvement effort, try to get action teams involved in rapid learning cycles within two to three weeks after concluding a mapping exercise. Craft quick wins and 30-, 60-, and 90-day plans for implementation, but think about a future state that is 18 to 24 months out. In other words, nest those short-term improvement efforts in the context of a longer-range vision. That way, people have some sense of where they’re headed, and you have insurance against doing improvement work that optimizes some portions of the value stream but sub-optimizes others.
7. Count, Count, Count — But Count the Right Things
Before you start, be clear about the “vital signs” for your value stream — the few key metrics that tell you whether the value-stream performance is healthy — and the key few metrics for the individual processes that make up that value stream.
Be sure to measure things that are meaningful to the people doing the work, allowing them to see the improvement and how their work links back to the higher-level organizational goals and metrics. Use existing information systems when you can, but you may need to measure manually when you are getting started. If so, keep your measurements simple. Otherwise, they won’t get done — or done honestly.
8. Experiment Before You Implement
Insist on experimentation. Establish a ground rule that no “solution” gets implemented hasn’t been tested to confirm that it will address the problem for which it was identified.
9. Don’t Be Afraid to Take It Outside
Some of the most critical value stream redesigns involve working across functions and organizations. Indeed, here’s where value-stream mapping comes into its own. Many organizations jump from a current state map to point kaizen improvement. However, when value-stream mapping cross-functional or cross-organizational value streams, ensure all key stakeholders agree on the key problems that need to be solved and reach a consensus on the future-state vision (in the form of a map). Agreement on a vision that eliminates or addresses those problems turns value-stream mapping into a powerful tool for system-level problem-solving.
10. Make It Fun! (Or at Least Not Painful)
I’ve already alluded to the importance of engaging people in improvement activities that are personally meaningful to them. However, we’ve seen many of our client organizations get downright creative regarding engaging staff members in the socialization of maps and improvement plans and involving them in rapid learning experiments. Such efforts include:
- communicating updates at shift-change spaghetti suppers or casino nights
- using unique themes (often involving sports) for obeya boards and board meetings
- posting pictures of employees involved in the work
- providing recognition for people who have gone above and beyond in the improvement efforts.
My all-time favorite is still a communication-board series with a movie theme for a general radiology workflow. It used “Playing Now” for the improvement effort underway, “Coming Attractions” for scheduled workflows to be improved, and “Critic’s Corner” for staff member comments about experiments and problems.
Ultimately, value-stream maps can tell a story — and tell it effectively. But a well-planned and executed value-stream mapping exercise that engages the right people and involves appropriate follow-up can change that story in ways that make a real difference for the long haul — in value stream performance and teamwork.
Editor’s Note: This Lean Post is an updated version of an article published on May 19, 2015, one of the most popular posts about this vital lean practice.
Learning to See Using
Value-Stream Mapping
Develop a blueprint of improvements that will achieve your organization’s strategic objectives.
Thank you for this post. The section on making sure the map stays in scope is very useful! I have struggled with this exact issue before and that explanation cleared it up.
What are your insights on capturing many kaizen bursts during process gemba? I have had various positive and negative feedback. I am believer of capturing all gaps and wastes as they are communicated and assign to the process affected.
To me not doing it is feedback not captures, opportunity not addressed.
But, some feedback I have received is that it is done at design level, do not overcomplicate the VSM.
Insights, please. Thanks!